在追求高精度、高效率的现代汽车制造业中,机器视觉正在逐步渗透到汽车生产的冲压、焊接、涂装、总装等全流程中。这项技术通过模拟人类视觉与认知能力,结合算法与硬件的协同,不仅解决了传统人工检测的痛点,更成为智能制造转型的核心驱动力之一。
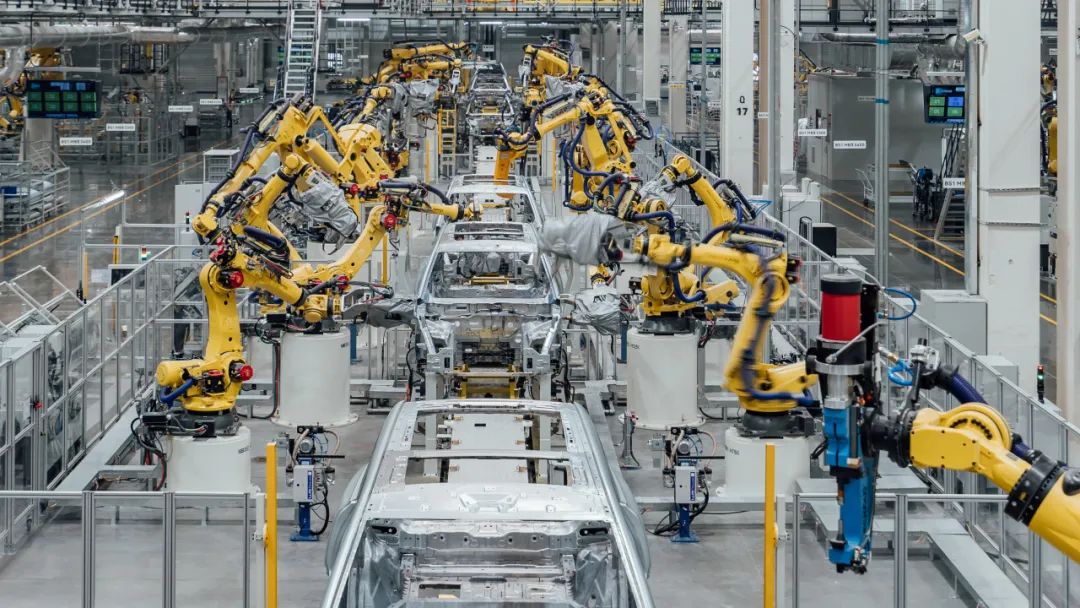
在汽车生产过程中,微小缺陷可能导致重大安全隐患。机器视觉通过高分辨率相机与AI算法,能精准识别车身涂装的划痕、凹陷,以及发动机缸体沙眼、活塞卡环错位等缺陷。以国内某知名车企为例,在引入创视自动化视觉检测方案后,发动机装配缺陷率降低90%以上,且系统可7×24小时无间断工作,避免人工疲劳导致的漏检。传统卡尺测量效率低且易受主观误差影响,而机器视觉采用3D扫描技术,可非接触式测量零部件的长宽高、孔径等参数,精度达微米级。例如,动力电池的毛刺检测、刹车片平面度测量等场景中,视觉系统能实时反馈数据,确保装配严丝合缝。
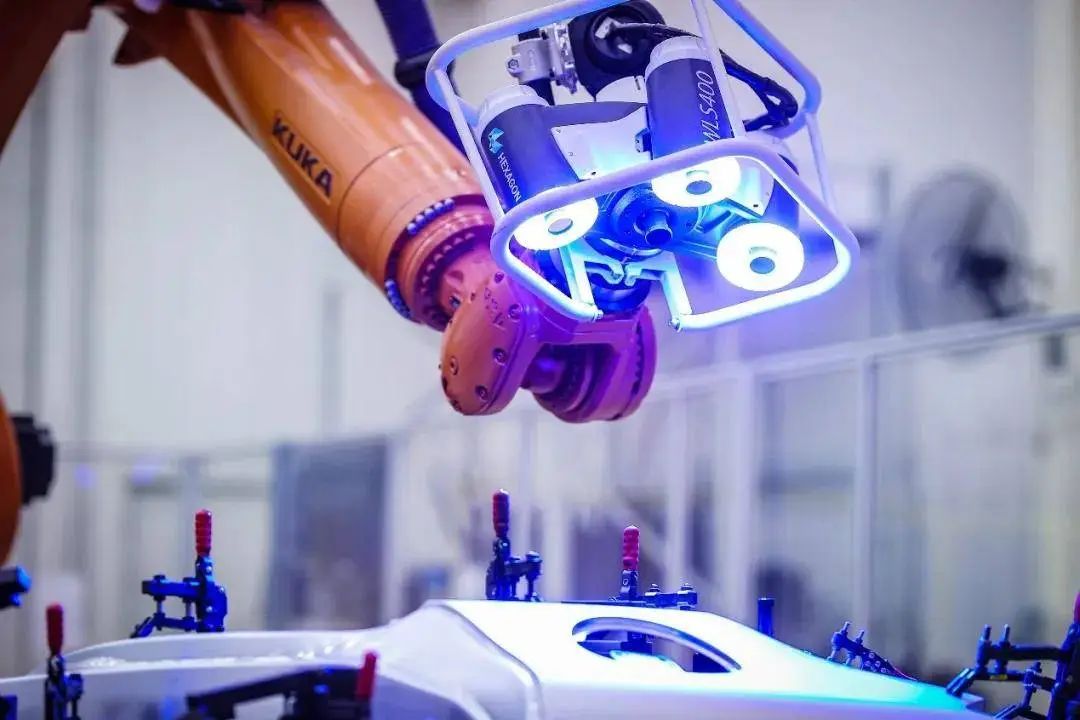
在汽车自动化产线的生产过程中,机器视觉引导机器人完成高难度动作:如通过实时焊缝跟踪修正焊接路径,或在风挡玻璃装配中精准定位抓取点,误差小于0.1毫米。这种灵活性使车企能快速切换车型产线,适应市场需求变化。从零部件打码到整车出厂,视觉系统记录每一环节的数据。例如,通过OCR识别零件编码,追溯缺陷源头;或监测涂胶工艺的连续性,防止因胶体断点导致密封失效。
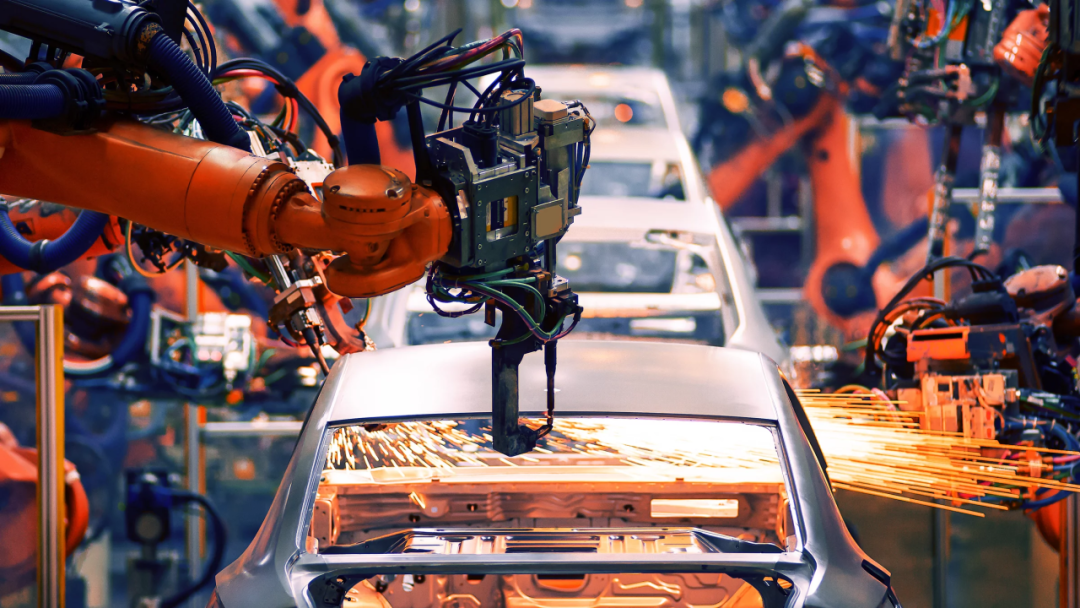
人工检测单个零部件需数分钟,而视觉系统仅需50-200毫秒。以国内某新能源电池厂为例,在采用创视自动化视觉集成方案之后,采用视觉检测,单线日产能提升40%,同时减少50%的质检人力。视觉检测初期投入虽高,但长期可节省培训、误检返工等隐性成本。据统计,车企在采用创视自动化视觉检测方案后,质量管控成本平均降低35%,且设备寿命可达8-10年。
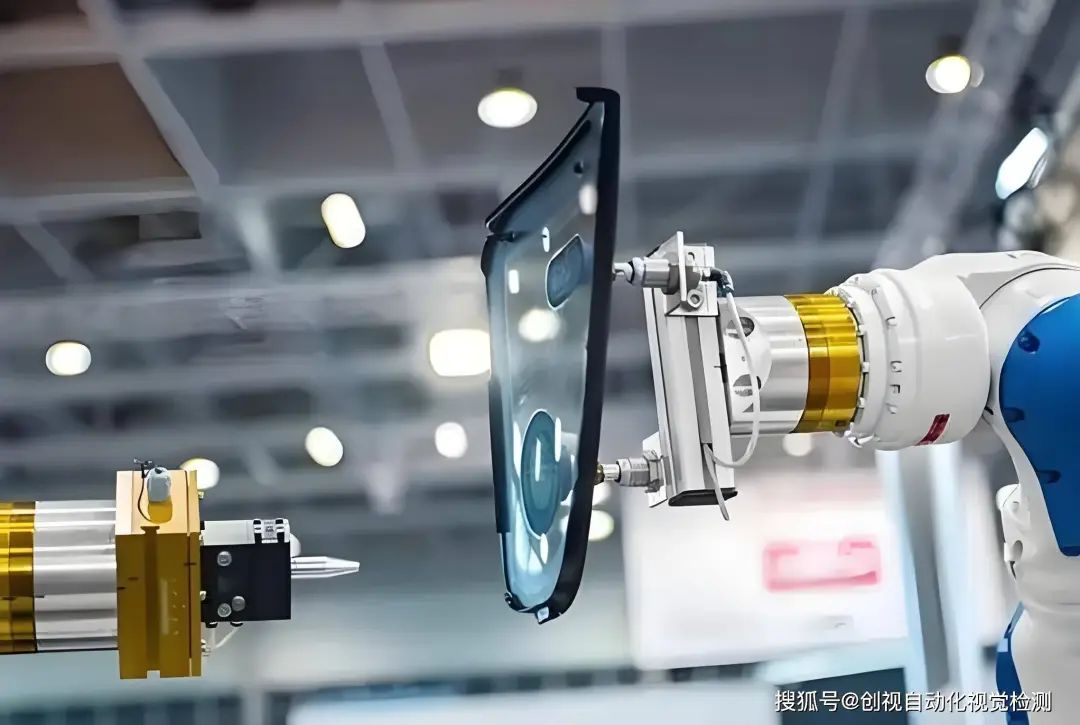
在高温焊接车间、粉尘弥漫的铸造区,机器视觉替代人工进入危险环境。例如,通过红外光源检测发动机缸套内部缺陷,或利用抗干扰算法在强振动环境下完成螺栓紧固验证。
尽管机器视觉已取得突破,但仍面临复杂光照干扰、微小特征识别瓶颈等问题。例如,深色车漆表面的划痕检测需特殊光源设计,而透明挡风玻璃的瑕疵识别依赖多光谱成像技术。未来,三大趋势将重塑行业:

从“制造”到“智造”,机器视觉检测已不是简单替代人眼,而是通过数据闭环驱动工艺优化。随着国产视觉系统在算法、光源等核心环节的突破,中国汽车产业正借助这项技术,在全球竞争中加速超车。