在现代工业制造体系里,螺丝尺寸小,但在电子设备、汽车制造、机械加工等领域中承担极为关键的连接与紧固重任,直接左右产品整体性能与安全。然而,传统螺丝生产流程中缺乏有效的缺陷检测手段。随着机器视觉检测技术的兴起,特别是创视推出的多面外观检测设备在各企业中的逐步应用,为螺丝表面缺陷检测开辟创新且高效解决途径。
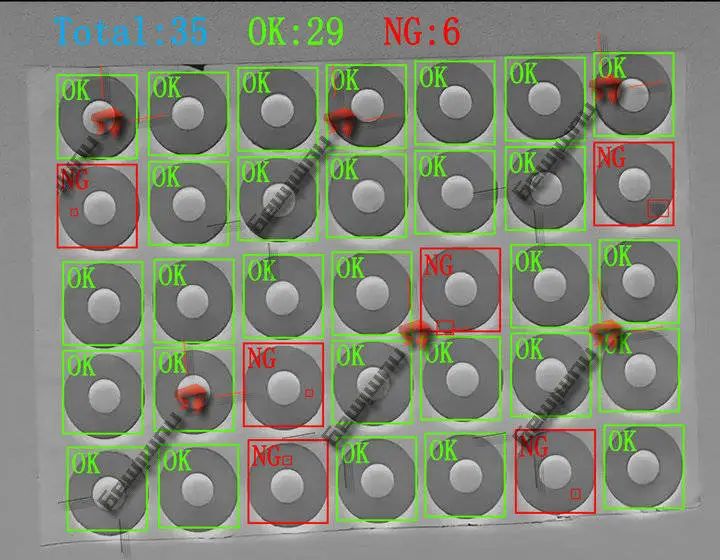
现代化工厂内,螺丝每分钟可以生产数百甚至上千颗。人工检测要求工人长时间全神贯注,逐个查看流水线上的螺丝,面对几块的生产速度,人工检测难以契合大规模、高速生产的需求。
人工长时间进行重复工作时,容易感受到疲劳,并且注意力下降,导致漏检、误检情况频发。据统计:人工检测螺丝缺陷的准确率在80% - 90%左右,难以保证产品高质量。
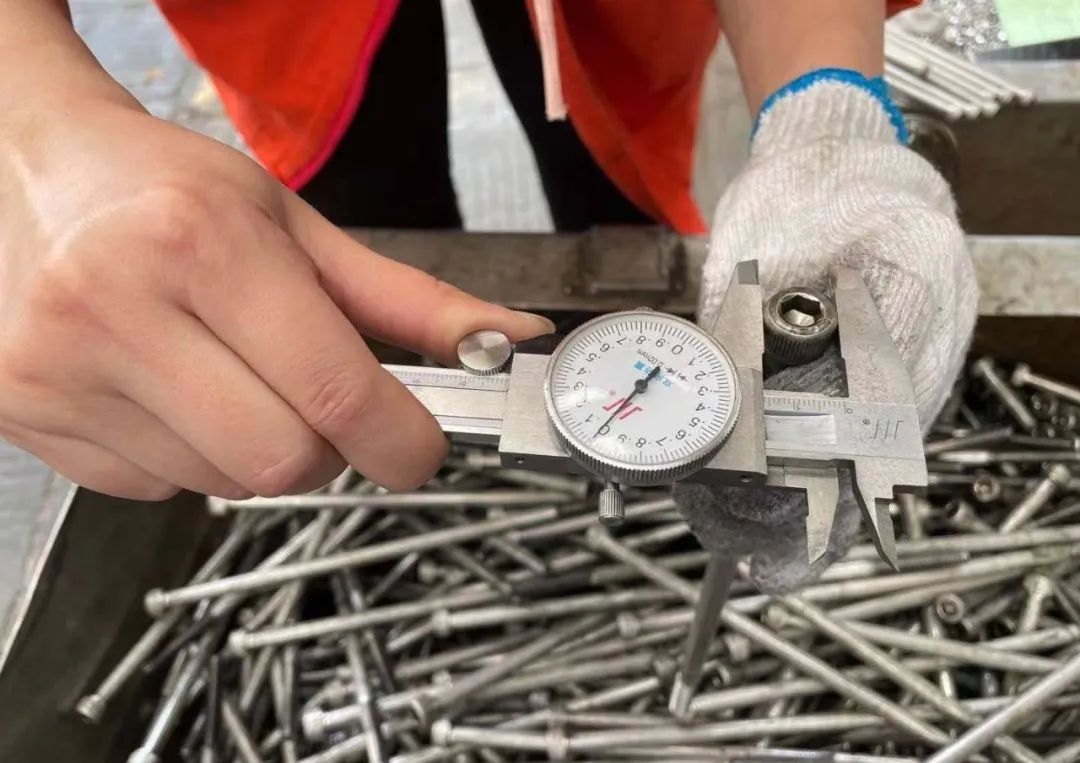
机器视觉视觉成像系统主要由相机、镜头、光源等系列光源成像硬件构成。其中光源的设计尤为关键。采用环形光源能够均匀照亮螺丝表面,清晰呈现螺纹细节;点光源则可以聚焦照射螺丝头部,强化细微裂纹与正常表面的对比度。相机在镜头的协同下,快速抓取螺丝的高清图像,并传输至图像处理软件。

采用创视工业视觉软件,针对螺纹缺陷检测,算法通过检测样品与与标准螺纹图像对比,精准计算螺距、牙型角等参数,以此判断螺纹是否完整、符合规格。遇到螺丝头部变形的情况,软件借助形状识别算法,与预设的标准形状比对,迅速识别出变形部位及程度。检测裂纹时,依据图像灰度值的变化,精确确定裂纹位置并测量其长度和宽度。
设备基于先进视觉检测技术,具备高精度、高效率、广泛通用性等特点,内置深度学习算法模型。能够对螺丝进行360度无死角拍摄,确保螺丝表面任何细微缺陷都无处遁形。依据分析结果,设备通过机械控制系统对元件进行分类或分拣,不合格品将被剔除或分类存放,而合格品则继续流向下一道工序。

设备工作频率1200赫兹,处理速度可达8000件/分钟。采用高精度导料块和DD马达,平整度达到0.02mm,支持多种产品的尺寸测量及缺陷检测。同时,设备以单机形式存在,便于安装调试与灵活配置,全面满足工业生产中的高品质检测需求。在电子设备制造、汽车制造等行业,机器视觉技术为螺丝质量把控提供了坚实可靠的保障,有效减少产品故障,提升产品品质。随着工业 4.0 和智能制造的持续推进,机器视觉在螺丝缺陷检测领域将不断与人工智能、大数据等前沿技术深度融合,进一步提升智能化程度,助力制造业朝着智能化、高效化大步迈进。